Create the
shape of
things to come.
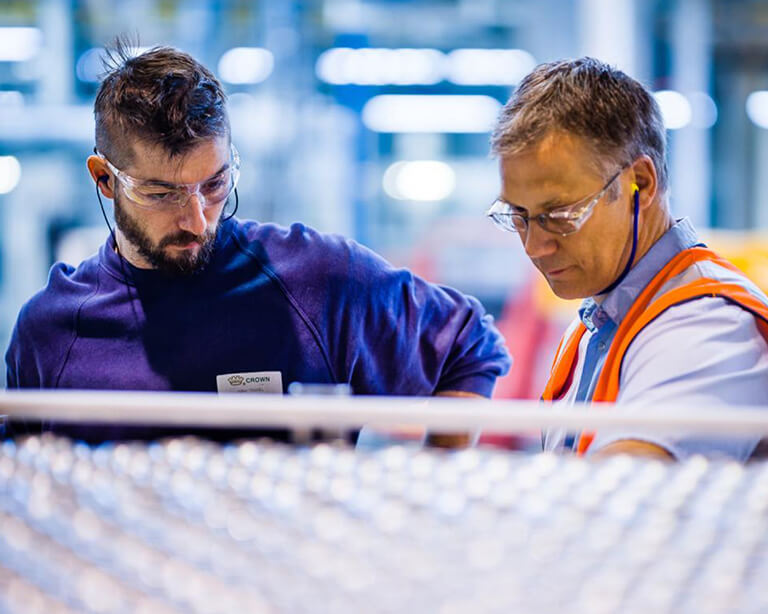
SR MANAGER, TOTAL QUALITY
Tampa, Florida Job Title Quality Job Type Salary Career Level Experienced (Non-Manager) Education Bachelor's DegreeAbout Crown:
CROWN Cork & Seal USA, Inc., a wholly owned company of Crown Holdings, Inc. is a global leader in the design, manufacture, and sale of packaging products for consumer goods. At Crown, we are passionate about helping our customers build their brands and connect with consumers around the world. We do this by delivering innovative packaging that offers significant value for brand owners, retailers, and consumers alike. With operations in 39 countries employing approximately 25,000 people and net sales of approximately $12 billion, we are uniquely positioned to bring best practices in quality and manufacturing to our customers to drive their businesses locally and globally. Sustaining a leadership position requires us to build a team of highly talented, dedicated, and driven individuals.
A Sr Quality Manager is responsible for overseeing the development, implementation, and monitoring of quality management systems in an organization to ensure products or services meet or exceed customer expectations. This role requires a focus on continuous improvement, efficiency, and customer satisfaction through strategic planning, process management, and cross-departmental collaboration.
The position will require approximately 80% travel throughout US. There is some flexibility with regard to where the position will be based. A location in the Midwest would be preferred or close to Crown Manufacturing sites.
Key Responsibilities:
- Develop and Implement Quality Management Systems:
- Establish and maintain the organization’s QMS in alignment with industry
- Implement quality standards, policies, and procedures to ensure compliance and continuous improvement.
- Leadership in Quality Strategy:
- Develop and drive the organization’s quality strategy, goals, and vision in collaboration with senior management.
- Lead initiatives to improve operational efficiency, reduce costs, and improve product and service quality.
- Process Improvement:
- Use tools such as Six Sigma, Lean, or Kaizen to identify areas for process improvement.
- Analyze current business processes, identify inefficiencies or defects, and recommend and implement solutions.
- Quality Audits and Inspections:
- Lead internal audits, inspections, and assessments to ensure compliance with quality standards.
- Work with external bodies or clients to ensure that quality audits and inspections meet regulatory standards.
- Audit Plants for with regard to Policy, SOP, PCR checks and compliance.
- Employee Training and Development:
- Develop and deliver training programs on quality management principles, tools, and techniques for employees at all levels.
- Encourage cross-functional collaboration and promote quality awareness throughout the company.
- Data Analysis and Reporting:
- Collect, analyze, and interpret quality data to track performance and identify trends.
- Prepare and present monthly reports on quality metrics, key performance indicators (KPIs), and continuous improvement progress to management. Implement & Track Corrective actions for improvement
- Technical writing skills provide an advantage in report development and team progress.
- Customer Satisfaction:
- Monitor customer feedback and work with teams to address quality-related issues.
- Implement strategies to improve customer satisfaction and enhance the company’s reputation for quality.
- Customer visits when necessary
- Supplier and Vendor Quality Management:
- Work with suppliers and vendors to ensure the quality of materials, components, and services meets organizational standards.
- Compliance and Regulatory Requirements:
- Ensure adherence to industry regulations, standards, and laws related to quality management.
- Prepare for and manage external quality certifications and audits.
- Personal Attributes:
- Positive Attitude
- Able to work cross functionally and support with Team Members (Corp & Plant).
- Attention to detail and a commitment to excellence.
- Ability to drive change and lead organizational transformation.
- Strong decision-making skills based on data analysis and empirical evidence.
- A proactive and results-oriented approach.
Job Requirements
Skills & Qualifications:
- Education: Bachelor's degree in Business, Engineering, Manufacturing, or a related field (Master's or advanced certifications in quality management preferred).
- Experience: At least 5-7 years of experience in quality management or a related role, with a minimum of 3 years in a managerial or leadership position.
- Certifications: Certified Quality Manager (CQM), Certified Quality Auditor (CQA), or Six Sigma certifications (Green Belt, Black Belt) are a plus.
- Skills:
- Strong leadership and team management skills.
- Excellent problem-solving and analytical abilities.
- In-depth knowledge of quality management systems and methodologies.
- Proficiency in quality improvement tools such as Root Cause Analysis, Fishbone Diagrams, Failure Mode Effects Analysis (FMEA), etc.
- Strong communication and interpersonal skills for collaborating with teams and management.
The Total Quality Manager plays a crucial role in ensuring the company’s products and services maintain the highest quality standards, contributing to customer satisfaction, operational efficiency, and overall business success.
· Providing Technical Quality Support to Plant Management Teams and plant personnel with regard to all quality issues. This will include guidance and direction with respect to managing our production processes and implementation of best practices from a Quality perspective.
· Ensuring conformance to the published quality standards, using approved standard operating procedures, and certified gauges/measuring instruments.
· Ensuring the validity of various operating process specifications – product dimensional specifications, and directing the plant quality managers in the area of ensuring conformance to customer specifications/requirements.
· Working closely with our Sales team on business development needs and quality issues that arise with customers.
· Collaborating with the subgroups in Corporate Technologies to ensure that new specifications/materials or processes meet or exceed the Crown requirements as well as fit our manufacturing process capabilities.
- Conducting plant audits of our domestic manufacturing facilities and on occasion of our suppliers.
· Providing specific quality training to employees in SPC techniques, 5S, SMED, GMP, problem solving and personal development training, as well as providing for the development of on-the-job training, as required.
Explore this location
View Map- Stacker Operator Manufacturing and Production Crawfordsville, Indiana
- Electrician - Hourly Manufacturing and Production Conroe, Texas
- Back End Maintainer (Production Mechanic) Manufacturing and Production Weston, Ontario
- Maintenance Technician/ Electrician 2nd shift Manufacturing and Production Dubuque, Iowa
You have no Recently Viewed Jobs. View all available opportunities.
There are currently no open jobs near you. View all available opportunities.